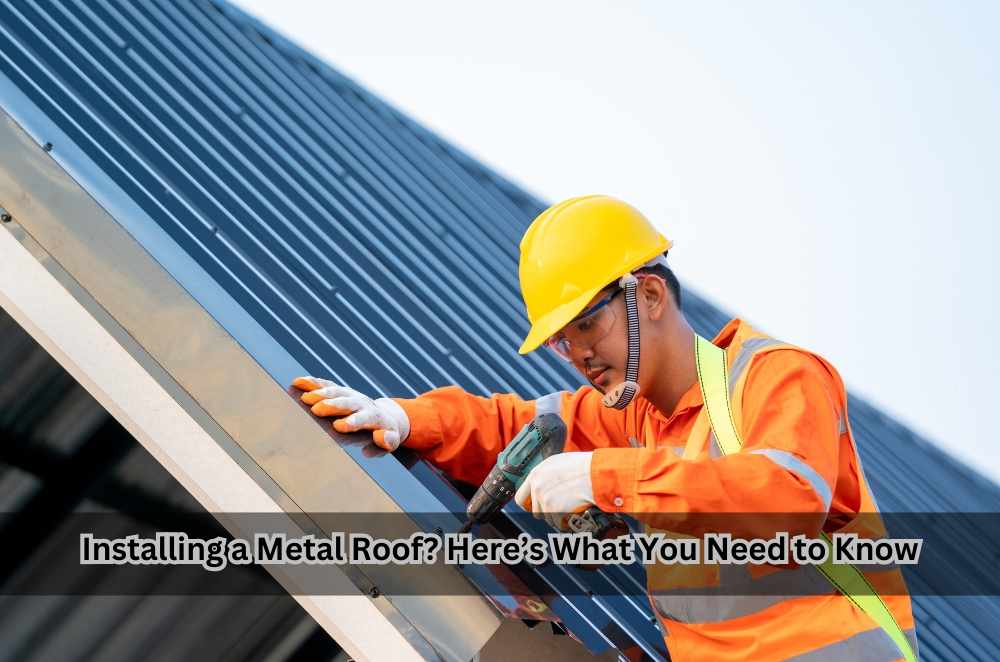
Metal roofing has become a popular choice across Australia, and for good reason. But when it comes to metal roof installation, there’s a lot more to it than simply laying sheets and calling it a day. Known for its durability, energy efficiency, and modern design appeal, it’s more than just a functional upgrade. But installing a metal roof isn’t as simple as laying down sheets and calling it done. From planning approvals to material selection, the process demands a thoughtful, informed approach.
Whether you’re building new or replacing an older roof, understanding how metal roofing works and what pitfalls to avoid can save you time, money, and stress.
Why metal roof installation is worth considering
Metal roofing isn’t just a trend, it’s a long-term investment. Homeowners across the country are making the switch for reasons that go beyond curb appeal.
Based on what I’ve seen on the job, many are surprised by the immediate comfort improvement. One client told me their house was noticeably cooler just days after their metal roof went up, thanks to its reflective coating.
Key advantages include:
•Longevity: A properly installed metal roof can last 40+ years with minimal upkeep.
•Toughness: Built to withstand Australia’s harsh climate, from coastal salt spray to bushfire zones.
•Lightweight: Places less stress on your home’s structure compared to heavier roofing like tile.
•Energy efficient: Reflective finishes help reduce heat absorption and lower cooling bills.
It also looks the part—modern metal roofing now comes in a range of colours and finishes that suit everything from rural homesteads to sleek city builds.
Planning is key: Design, permits, and materials
Think of metal roofing as a staged project. Before any sheets are laid, there’s a checklist of design choices, structural assessments, and permit approvals to work through.
I once worked with a couple in rural NSW converting a shed into a home. They were keen to get started but ran into council delays due to an incorrect wind classification. A bit of early planning could’ve saved them weeks.
Your pre-installation planning list:
•Roof pitch and span: Determines which metal profiles and finishes are suitable.
•Permits and engineering sign-off: Especially important for new constructions or full replacements.
•Roof frame and insulation checks: Consider if you’ll need new battens, sarking, or insulation upgrades.
•Choosing the right material: Colorbond, Zincalume, Galvanised steel—each has unique benefits and ideal use cases.
For accurate guidance on permits and compliance, refer to Australia’s national building standards
What to expect during installation
A professional team can typically install a metal roof within 2–5 days, depending on the roof’s complexity. It’s faster and cleaner than tiling, but not without its own technical demands.
The usual installation stages look like this:
•Tear-off phase: If you’re replacing an old roof, removal is the first step.
•Structural inspection: Check for issues like rotten timber, sagging, or damaged battens.
•Sarking and battens: New vapour barriers and battens might be needed before the sheets go on.
•Sheet laying: Panels are fixed starting from the eaves, overlapping for waterproofing.
•Flashing and sealing: Precision work around ridges, valleys, and penetrations prevents leaks.
During one Melbourne job, a surprise rainstorm hit halfway through the install. We had to tarp half the roof in a rush, so yes, always have a wet-weather backup plan.
Mistakes to avoid when installing a metal roof
Even experienced teams can get it wrong if they cut corners. From my own experience, these are the most common (and costly) mistakes I’ve seen:
•Overtightened screws: This distorts the metal and creates leak points.
•Poor sealing around skylights: A frequent culprit for future water ingress.
•Metal incompatibility: Mixing certain metals causes electrochemical corrosion over time.
•Bad ventilation design: Traps heat and moisture, potentially damaging insulation or roof timbers.
And if you're planning with resale in mind, here’s how a roof upgrade can significantly improve your property’s market appeal with the practical metal roofing strategy.
Budgeting and protecting your investment
The upfront cost for a metal roof ranges between $80 and $150 per square metre installed, depending on materials and complexity. While this may seem steep, the low maintenance and extended lifespan often make it the smarter financial decision over time.
To get the most from your investment:
•Hire licensed professionals – Check references, reviews, and previous project photos.
•Register your warranties – Especially for high-end materials like Colorbond.
•Keep valleys and gutters clean – Prevents rust and corrosion from organic build-up.
Sustainable choices and future upgrades
Metal roofs are one of the most environmentally sustainable options available. Not only are they recyclable, but many products are already made from reclaimed steel or aluminium. And they pair perfectly with other green upgrades.
One client recently added solar panels straight onto their new steel roof. The installers noted how much easier it was compared to mounting on old tiles.
If sustainability is your goal:
•Choose high-reflectivity coatings: These boost energy efficiency even further.
•Think solar and water harvesting: Design your roof for add-ons.
Use recyclable materials: Most modern metal roofs tick this box by default.
Final thoughts
A metal roof isn’t just a protective layer, it’s a long-term improvement for your home’s durability, energy performance, and resale value. But success hinges on getting the details right from the start.
•Ask questions early
•Check your approvals
•Vet your installers
•Don’t rush the job
One last tip? Compare multiple quotes and ask every roofer about their metal-specific experience. That extra prep can save you thousands down the track. Once installed, your metal roof will work hard for decades—quietly, efficiently, and without much fuss.
Write a comment ...